How Balancing Truck Tires Helps the Bottom Line
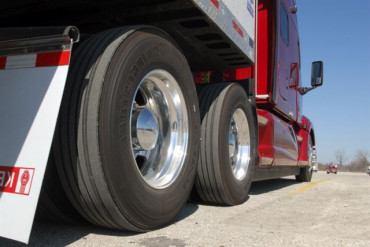
Tire balancing has changed over the years – both the techniques used and the reasons for doing it. If you're not balancing your tractor and trailer tire and wheel assemblies, you could be leaving money on the table
While cleaning out my garage recently, I came across several 5-gallon buckets of lead wheel weights sitting next to a manual tire machine and single-plane static balancer that served me well for decades. I originally got these tools to keep the typical, often-untrained service-station mechanic from damaging my prized alloy wheels – or simply not paying attention to the fine details of balancing, such as splitting weights between the rim flanges based on rim width and offset.
It made me think about just how far our industry has come in tire balancing technology. Most consumer tire stores now have new-generation mounting machines that don’t even contact the wheels, and dual-plane, software-run balancers that distribute the weights to accommodate the variety of rim widths, offsets, and even flangeless wheels. The more amazing observation is that the tires and wheels themselves are more uniform than in the past, requiring less corrective action to reduce vibration and increase tire life.
Progress in the commercial truck tire/wheel balancing market has been of a different sort, but even more impressive in its own way. First, the advances in tire reliability and uniformity are particularly impressive, especially if you are a tire engineer, as I am, with a little history to enhance your perspective. Second, a large-scale switch to more precision-forged aluminum wheels, instead of steel, on power units have resulted in trucks that rarely vibrate enough to cause driver ride complaints, even in high-speed linehaul service.
Given these advances, you may wonder if balancing truck tire/wheel assemblies is going the way of the buggy whip. In fact, balancing wheels on commercial vehicles is not only very much alive, but also is likely to grow rapidly in the next few years.
How Balancing Technology is Changing
The traditional method of attaching weights to wheels to balance the assembly has some shortcomings:
1. A typical 295/75R22.5 drive tire loses just over 30 pounds between when it's new and when it is removed for retreading at or near the industry average of 6/32 tread depth remaining. This means the initial balance correction becomes less accurate as the tire wears – and often actually creates imbalance in later tire life. Rebalancing is often not a viable option in modern maintenance scenarios due to shop costs, downtime, maintenance outsourcing, road services, and other logistics issues. This can result in ride issues, but more likely creates the onset of irregular wear, and finally adversely affects fuel economy.
2. Lead is currently outlawed in Europe and in several states as a toxic metal. This prohibition is expected to expand, and responsible disposal of used weights is becoming a new environmental issue. It is true that other materials such as tin, steel, and zinc may be substituted, but all require a physically larger weight, and this can adversely affect the wheel weight’s ability to remain on the rim flanges. Wheel weight retention on aluminum wheels is already a widely recognized problem in the trucking industry. Further, there is a galvanic corrosion issue when weights contact bare aluminum. This has become a larger issue with the more aggressive and corrosive chloride types of anti-icing chemicals that are rising in usage.
The most desirable material for balancing would be non-toxic, have no attachment issues, not corrode or otherwise harm the tire or wheel surfaces contacted, and would be adaptive to compensate for the rotating mass reduction as tires wear in order to maintain correct balance through the entire tread life, along with the variations in load, speed, and road conditions that the tires experience.
Such materials do now exist from several manufacturers. These materials are typically placed inside the tire when mounting and essentially re-balance the rotating assembly each time the vehicle rolls after a stop. Since the least expensive and easiest method of installing these materials is when mounting new tires, some fleets have arranged for truck and trailer manufacturers to do this at the factory.
Many fleets have begun using these internal balancing materials with good results. They report better truck ride, fewer driver complaints, reduced irregular tire wear in later wear stages (leading to extended takeoff mileages), and overall reduced tire program costs. (The American Trucking Associations’ Technology & Maintenance Council’s RP 246 offers advice to help fleets choose the best product for their needs.)
In spite of this, many fleets currently balance few, if any, tire/wheel assemblies due to the absence of any ride issues. Understandable, but doing so leaves significant money on the table.
Balancing and the bottom line
Several TMC Type II fuel economy tests conducted by different companies have shown a fuel economy advantage of an average 2.2% for tractor-trailers with 18 wheels using internal adaptive balancing versus unbalanced (but typical) assemblies with no exhibited ride issues. (See TMC RP 1111).
There has been lots of discussion among industry experts about how these tests relate to real world results where driver input, service conditions, and other operational issues affect wheel balance. But it is generally agreed that a fleet might reasonably expect to realize at least half of this fuel economy improvement by adopting adaptive tire balancing, especially in linehaul service.
Conversely, that means passing up a consistent fuel economy benefit of over 1% by not balancing tires.
Ironically, it’s the trailer axles that contribute most to fuel economy results, as stated in the recently revised TMC Recommended Practice RP 214, and these tires are traditionally the last to be considered for balancing. The good news is that trailer tires also wear slower than steer or drive tires, and therefore, the improved fuel economy derived by balancing them will be longer lasting.
After discussing these results with numerous engineers, the explanation is quite simple: Most rotating masses already on the truck are balanced, for reasons of either durability, long component life, or vibration reduction. All balanced masses experience less energy loss to surroundings (usually in the form of heat or sound) compared to unbalanced masses. Drive shafts, clutches, cooling fans, crankshafts, and piston and connecting rod assemblies are well-recognized examples of this engineering maxim. Tire and wheel assemblies are no exception. Balanced rotating assemblies conserve energy overall. It is also worth noting that major truck tire manufacturers now recommend balancing tires for optimum performance, recognizing that unbalanced assemblies can contribute to irregular wear and shortened removal mileages.
So there you have it. Stay ahead of the curve to improve fuel economy and consider balancing all tires, but especially trailer tires, with adaptive internal balancing materials. The cost is comparable to, or often less than, traditional balancing. The fuel economy payback should be an easy calculation and short term. All major tire manufacturers are familiar with these products and should be consulted to make sure that the mounting lubes and practices in your fleet are compatible. Better yet, talk with some of the longer-term users of these products to confirm their practices and experience. Keep the wheel weights out of the bucket and take the money saved off the table!
Asa Sharp was a tire engineer and marketing manager at Goodyear for 36 years. He is a longtime active member of ATA's Technology & Maintenance Council, a member of the S.2 Tire & Wheel Study Group, a TMC Silver Spark Plug recipient, and today he does independent consulting. This article was authored under the guidance and editorial standards of HDT’s editors to provide useful information to our readers.