Don’t Overlook These Trailer Maintenance Items
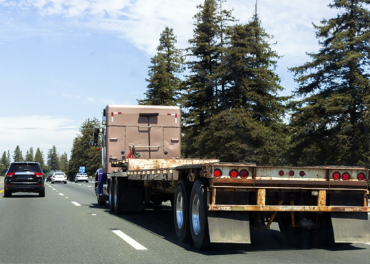
While a truck is the mule that pulls the cart, if your cart is broken, it doesn’t matter how big the carrot is — that mule ain’t moving. A good maintenance program needs to ensure that your trailer is up to snuff. But because trailers are often out of sight, out of mind, there are several areas that are often overlooked. We talked to fleet maintenance experts to uncover areas that may suffer from neglect.
A well-thought-out maintenance program and schedule is a must.
Heath Nace, fleet maintenance manager at Bethel, Pennsylvania-based K.L. Harring Transportation, believes trailers have been overlooked by many fleets for many years.
“I’ve seen service intervals all over the board for trailers,” Nace says. “I recommend setting trailer services up on a ‘days’ interval — every 180 days, for example — rather than miles or hours, as most don’t have a good means of tracking those parameters.”
Nace is not alone.
“It’s been said that a trailer fleet is the most neglected piece of equipment within any transportation company. To this day, I still believe that to be true,” says Jarit Cornelius, vice president of asset maintenance and compliance at Sharp Transport in Ethridge, Tennessee. “We learned early on that sticking to the program pays for itself in dividends.”
For Cornelius, there are two important factors that must be kept in mind: who is servicing your equipment, and what type of service quality is being performed, especially in the field with mobile trucks.
Automatic tire inflation systems should be checked regularly, ensuring the tire inflates to the correct pressure and there are no air leaks at the wheel-end.
Photo: Jim Park
“One trick I’ve used is keeping an eye on shop supply orders and specifically looking for grease zerks on the orders,” he adds. “Is the shop having to order them? Are they getting used? Contrary to what some may believe, these little things can and will go bad.”
Judging the Cover Before the Book
For Larry Olson, director of field maintenance for Ryder’s west region, pulling out the ladder and getting a closer look is at the top of his trailer to-do list.
“Don’t forget the top of the trailer, and ensure the tech has a safe ladder or inspection mirror on an extendable pole to view the integrity of the surface skin and attaching crimp or rivets,” says Olson, who also notes that basic things like lighting, leaks, and physical damage should not be forgotten.
While making your way around your trailer, don’t forget to give your rear underride guard a once-over as well, says Bruce Stockton, director of maintenance for Paul Transportation out of Tulsa, Oklahoma.
“In many cases, I see rear underride guards that may have met the requirement when [they were] built, but now [they’re] in violation of meeting the criteria due to corrosion, damage, or both,” says Stockton. “We’ve seen over the years that some trailers being built on the cheap from some manufacturers are using painted carbon steel that has corroded from the inside out, and while the bumper may look fine, serious corrosion has occurred, making them ineffective in a crash.”
Braking Bad?
Trailer brake and wheel-end inspections sometimes are not as thorough as they should be, whether during a driver pre-trip or in a shop PM.
“Check the operation of the brake chambers, rod travel, and calipers/shoes,” says Russell Brownfield, director of fleet maintenance at Altom Transport, an Indiana-based petroleum tanker carrier. Brownfield and his crew also use the Lite-Check 920, a trailer tester that drastically cuts down the troubleshooting time for antilock braking systems.
While not necessary every time, a bare-bones stripping down of all the components needs to be done to ensure drivers are getting the right amount of stopping power from the trailer braking system. Paul Cupka Jr., superintendent of the West Ox Maintenance Facility for Fairfax County’s Department of Vehicle Services in Virginia, has seen more than one culprit affect his solid waste transfer trailers, including the boots on the caliper tappets ripping and causing the calipers to seize.
Drivers have a role to play, too. Sometimes a simple pass by the driver can save time and money — and ensure the safety of the cargo, its driver and those around him/her — by simply checking the inside and outside of the wheel-end components for signs of fluid leaks or worn brake linings, which could lead to a failure, according to Ryder’s Olson.
“Between service events, the driver should also keep an eye on the brake lines that connect the tractor and trailer, and also all the lines feeding the brake components, as road debris could have impacted one of these items, and it requires a watchful eye at every opportunity,” he adds.
Don’t overlook the rear underride guard. It could be in violation of meeting performance criteria due to corrosion, damage, or both — something a plaintiff’s attorney could make hay with in the case of a tragic underride crash.
Photo: Jim Park
Adding Tech to the Mix
No longer boxes on wheels, trailers are increasingly seeing additional high-tech features that bring their own maintenance headaches, whether that’s trailer tracking, tire monitoring and automatic inflation systems, aerodynamic devices, camera systems, etc. With each installation come additional inspection items for your preventive maintenance program.
Some of that trailer tech can lead to maintenance warnings on the dash. “They share datalink connections with the tractor’s ECM protocol,” says Olson. “They can work in unison with each other, but be prepared for some learning curve and adapting your PM inspection list accordingly.”
After adding a handful of these technologies over the years, Cornelius says he’s had to stay on top of keeping his trailer services current.
“A good example would be with ATIS,” explains Cornelius. “Our technicians were responsible for retrofitting the majority of our trailer fleet several years ago, so they have a very in-depth knowledge of the systems, and how they are supposed to operate.”
Trailer services can check the ATIS by discharging air from the tires and allowing it to re-inflate. But did it re-inflate to the regulated psi? Were any audible air leaks noticed during operation? Did the low-psi light illuminate until the proper pressure was obtained?
“These systems are designed to save a company thousands on tires, but can end up costing you more if the system isn’t routinely inspected for optimal operation,” he says.
“Just having a preventive maintenance program is a huge advantage. From there, it’s about understanding the importance of routine inspections and ensuring your technicians are trained to treat PM services as the most important thing that can happen in any shop setting.”